Airless Spray Painting Pumps and Spray Guns
- PRODUCT
- Airless Spray Painting Pumps and Spray Guns
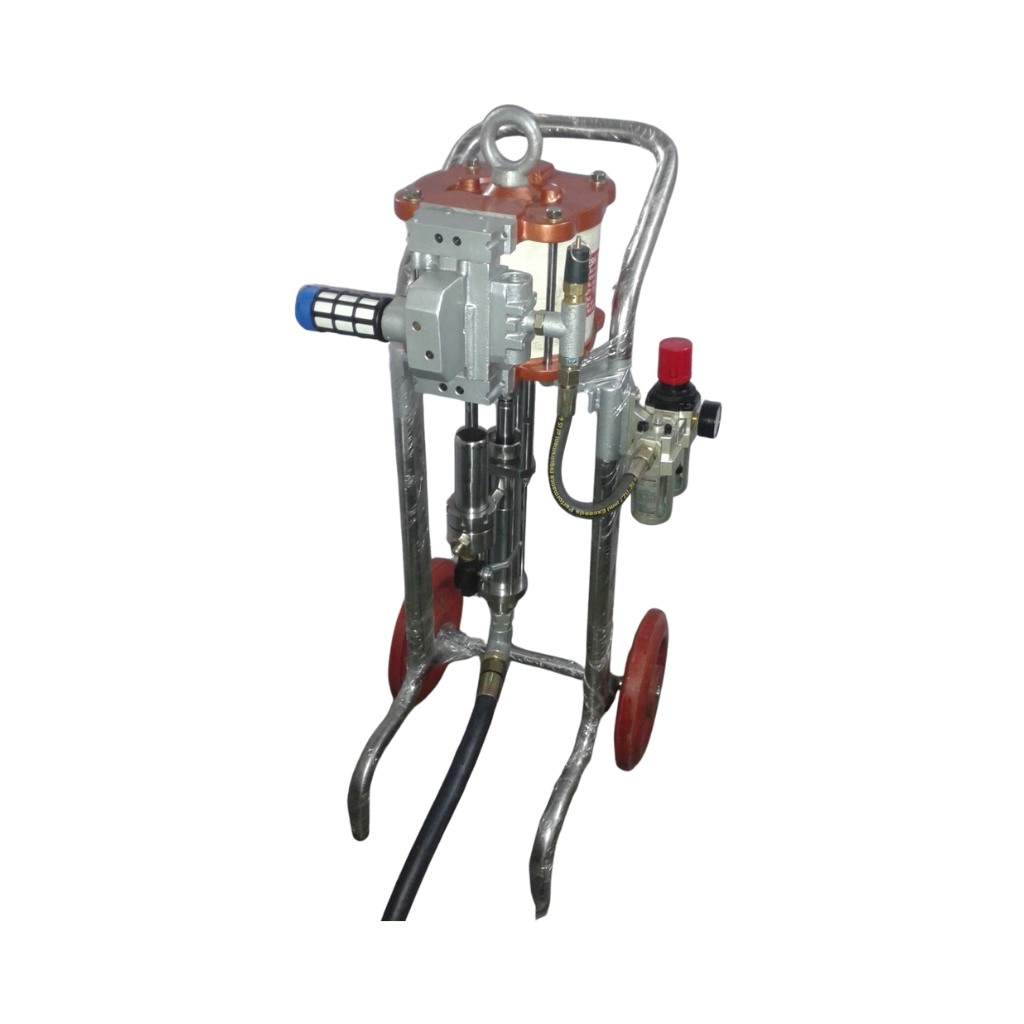
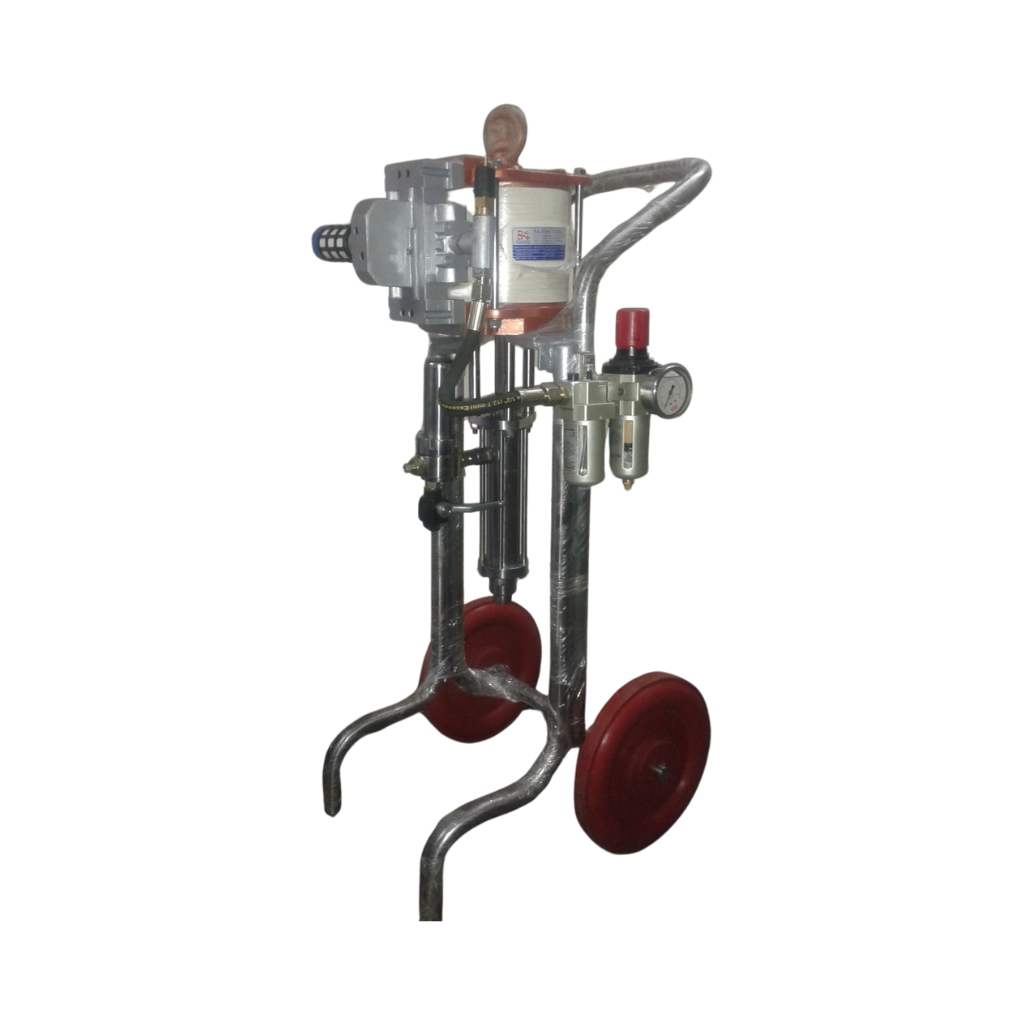
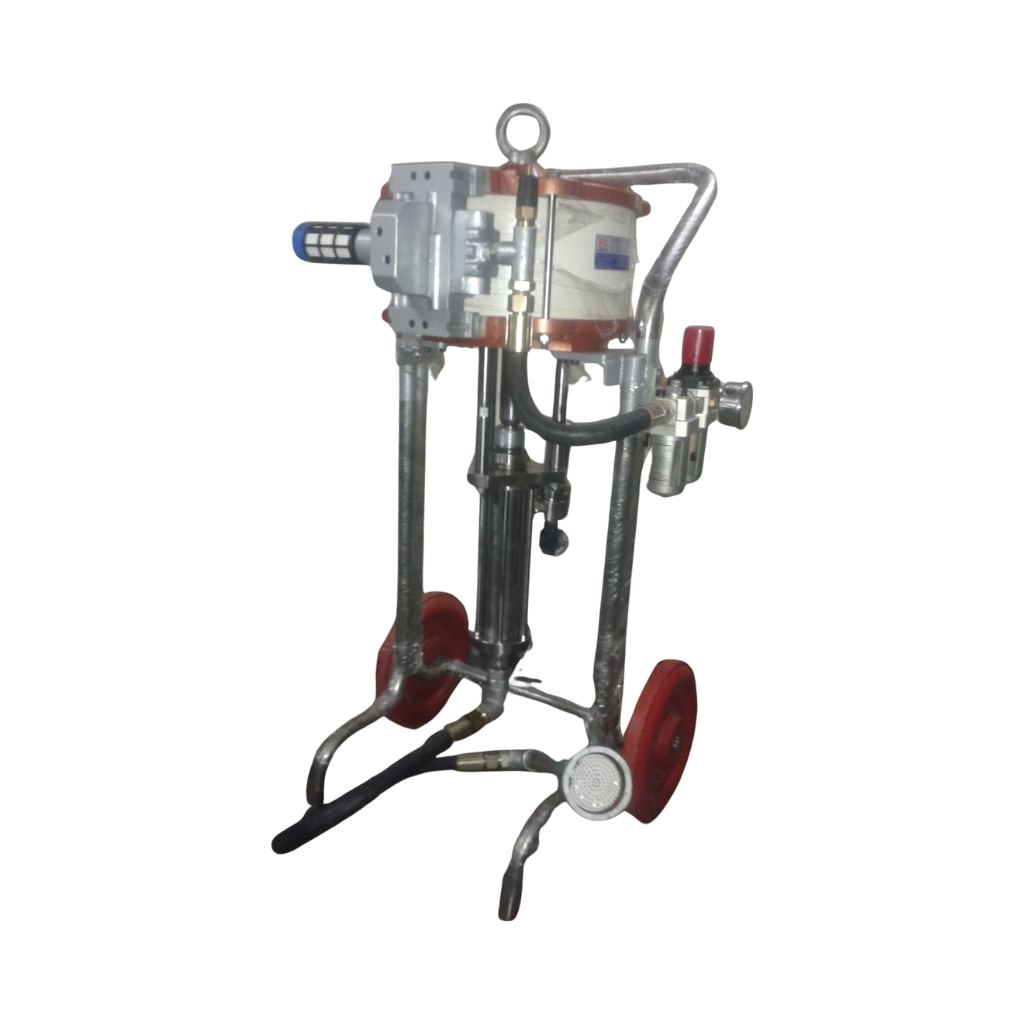
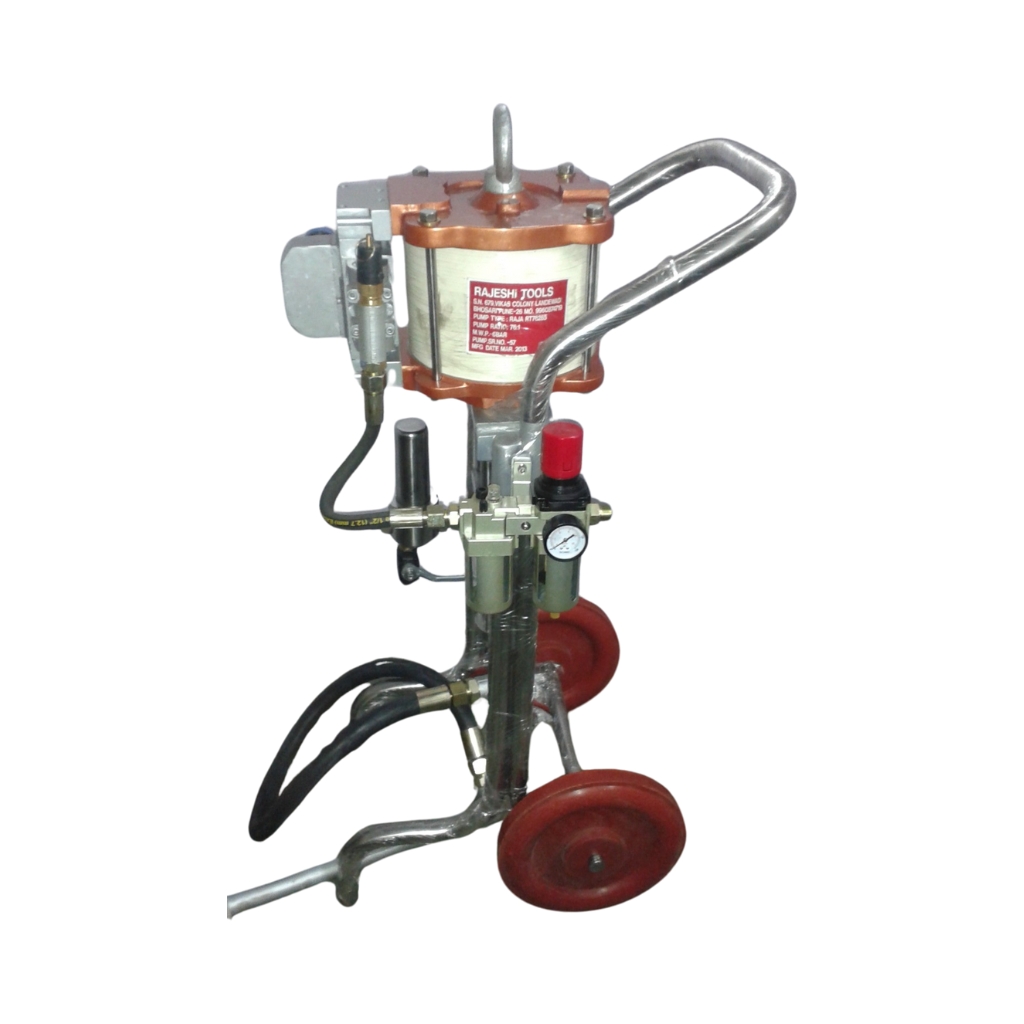
Total Airless Spray Painting Solution
Total airless spray painting is a technique used in the application of paint, coatings, or finishes onto various surfaces. It involves the use of specialized equipment that atomizes the paint into tiny droplets and propels them onto the surface using high pressure, without the need for compressed air. This method offers several advantages over traditional painting methods, including faster application, uniform coverage, and reduced overspray.
Spray Gun: The spray gun is the primary tool used to atomize and apply the paint. It consists of a nozzle, trigger, and handle. The nozzle is designed to break the paint into fine droplets for even distribution.
Pump: The pump pressurizes the paint and forces it through the spray gun. It may be powered by electricity, gasoline, or pneumatic energy.
Hose: The hose connects the spray gun to the pump and transports the pressurized paint to the gun. It must be durable and capable of withstanding high pressure.
Pressure Regulator: This component controls the pressure of the paint flowing through the system. It allows the operator to adjust the spray pattern and flow rate according to the requirements of the job.
Filters: Filters are installed in the system to remove any contaminants or impurities from the paint, preventing them from clogging the nozzle or causing defects in the finish.
Tip Guard: The tip guard protects the nozzle of the spray gun from damage and helps maintain the proper spray pattern.
Fluid Container: The paint or coating material is stored in a fluid container, which is connected to the pump for supply.
Safety Equipment: Personal protective equipment such as goggles, gloves, and respirators should be worn by operators to protect against paint fumes, overspray, and other hazards.
The process of total airless spray painting typically involves the following steps:
Surface Preparation: The surface to be painted must be clean, dry, and free of any contaminants or debris. It may need to be sanded, primed, or otherwise prepared depending on the type of material and desired finish.
Mixing Paint: The paint or coating material is prepared according to the manufacturer’s instructions, ensuring proper viscosity and consistency for spraying.
Setting Up Equipment: The spray gun, hose, and pump are assembled and connected, with the appropriate tip size and pressure settings chosen based on the requirements of the job.
Testing: Before beginning the actual painting process, the system is tested to ensure proper operation and spray pattern. Adjustments may be made to the pressure, flow rate, or spray pattern as needed.
Paint Application: With the equipment properly set up and tested, the operator begins spraying the paint onto the surface in smooth, overlapping strokes, maintaining a consistent distance and speed to achieve uniform coverage.
Drying and Curing: Once the paint has been applied, it must be allowed to dry and cure according to the manufacturer’s instructions. This may involve air drying or using additional curing methods such as heat or UV light.
Cleanup: After painting is complete, the equipment should be thoroughly cleaned to prevent dried paint from clogging the system. This typically involves flushing the pump, gun, and hoses with an appropriate solvent or cleaner.
Total airless spray painting is widely used in various industries, including automotive, construction, manufacturing, and marine, for applications ranging from large-scale projects such as painting buildings or bridges to smaller tasks like touch-ups and refinishing. Its efficiency, speed, and versatility make it a preferred choice for many painting professionals.